Forming Methods
One of the advantages of thermoforming is tremendous versatility coupled with reasonable costs. While material selection and tool design are variables that will contribute to producing the best part for the best value, the chosen forming technique is just as important. What follows is a brief description of the basic forming techniques and their relative advantages.
Drape Forming - Male
The plastic sheet is clamped in a frame and heated, then drawn over the mold - either by pulling it over the mold and creating a seal to the frame, or by forcing the mold into the sheet and creating a seal. Then vacuum is applied through the mold, pulling the plastic tight to the mold surface. In this method, the top of the part (area of the mold that contacts the plastic first) tends to be thickest, and the sides and lower portions that stretch and contact the mold last, tend to be thinnest.
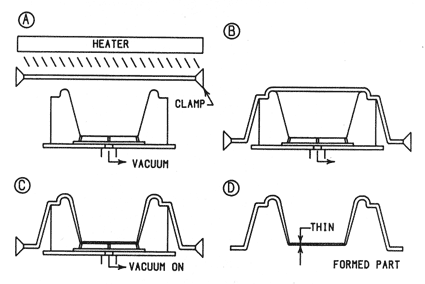
Snap-Back Vacuumforming - Male
After the plastic sheet is heated, a vacuum box seals to the clamping frame. Vacuum applied through this box pre-stretches the material by pulling it into a bubble. Bubble height is frequently controlled by an electric eye. When the plastic has been pre-stretched to the desired height, the mold enters the sheet and seals to the clamping frame. At that point vacuum is applied through the mold, and the vacuum box is allowed to vent to the atmosphere (or light pressure is applied in place of the vacuum). Very deep draws can be obtained with this system, and undesirable material thinning can be greatly minimized.
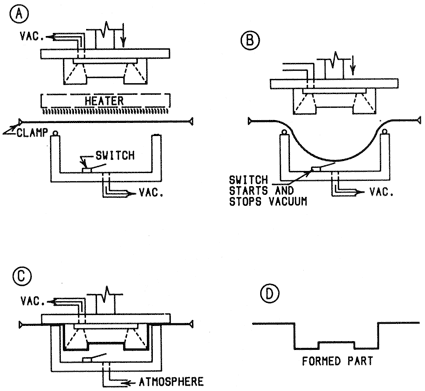
Billow Snap-Back Vacuumforming - Male
The heated plastic is clamped and sealed across a pressure box, then a bubble is blown toward the tool. Once the sheet has pre-stretched approximately 35 - 40%, the mold is forced into it while pressure behind the sheet remains constant. When the mold seals to the frame, vacuum is supplied through the mold. In some cases it may also be desirable to increase pressure in the pressure box at this point.
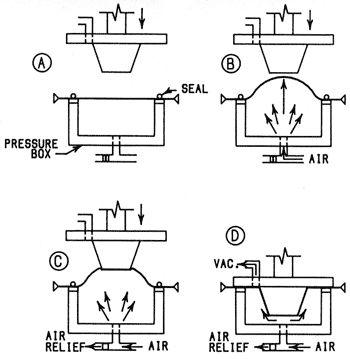
Straight Vacuumforming - Female
The heated plastic is clamped and sealed to the mold rim. Vacuum is then applied through the mold, causing atmospheric pressure to push the sheet down into the mold. As the plastic contacts the mold it cools. Areas of the sheet reaching the mold last are generally the thinnest.
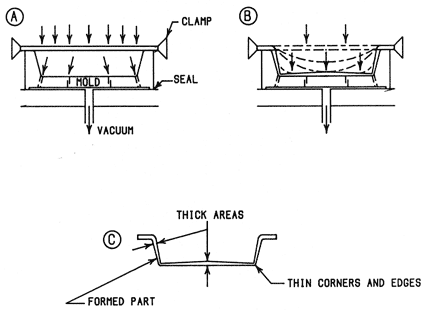
Plug Assist Vacuumforming - Female
After the plastic sheet is heated and sealed across the mold cavity, a plug shaped roughly like the mold cavity (but smaller) is plunged into the plastic sheet, pre-stretching the material. When the plug platen has reached its closed position, a vacuum is drawn through the mold to complete the formation of the sheet. Wall thickness can be varied by changing the shape of the plug. Areas of the plug touching the sheet first create thicker areas due to the chilling effect. Consequently, plug design is a critical determining factor in the geometry of the finished part being produced.
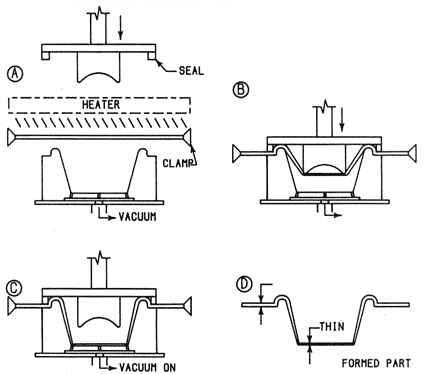
Plug Assist Pressure Forming - Female
Plug assist pressure forming is similar to plug assist vacuum forming, except that as the plug enters the sheet, air under the sheet is vented to the atmosphere. When the plug completes its stroke and seals the mold, air pressure is applied from the plug side. Plug temperatures are also important. By using the proper combination of plug design, plug temperature, and forming pressure, finished part wall thickness consistency can be greatly increased.
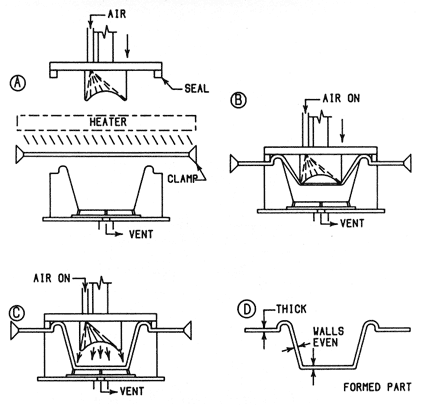
Billow Plug Assist Vacuum/Pressure Forming - Female
After the plastic sheet is heated and sealed across the female cavity, air is introduced into the mold cavity and blows upward toward the plug, forming a bubble that pre-stretches the material evenly. Height of this bubble is frequently controlled by an electric eye. A plug, shaped roughly to the contour of the cavity, plunges into the bubble. When the plug has reached its lowest position, a vacuum is drawn on the mold side to complete the formation of the sheet. In some instances, pressure forming air, supplied through the plug, is also used in this process.
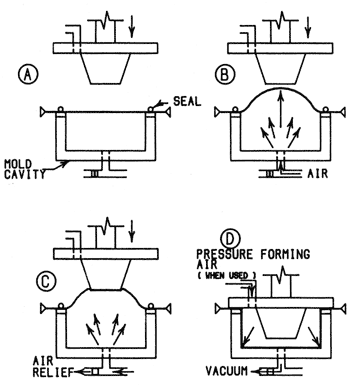
Pressure Forming - Heavy Gauge Sheet
Pressure forming is basically thermoforming with the addition of air pressure picking up the final details of a mold rather than relying on vacuum only. This process is used when sharp detail is required on the finished part. Using pressure forming, appearances equivalent to injection molding can be achieved on the mold side of the finished part.
A two-platen machine with strong closing power is required. The basic process of sheet clamping, heating and forming is the same as with conventional forming, but with the following exceptions:
- Air pressure, 20 to 80 psi, is used to blow the sheet against the mold
- The machine must have the ability to have the platens remain closed when the air pressure is applied
- Usually heated plug assists are required, and temperature controlled molds are a must
Pressure forming allows sharp radii, undercuts with sharp detail, textured tooling, and zero part draft. This is the recommended forming technique when the external aesthetics of injection molding are desired, but the part volume is insufficient to justify the injection molding tool cost.